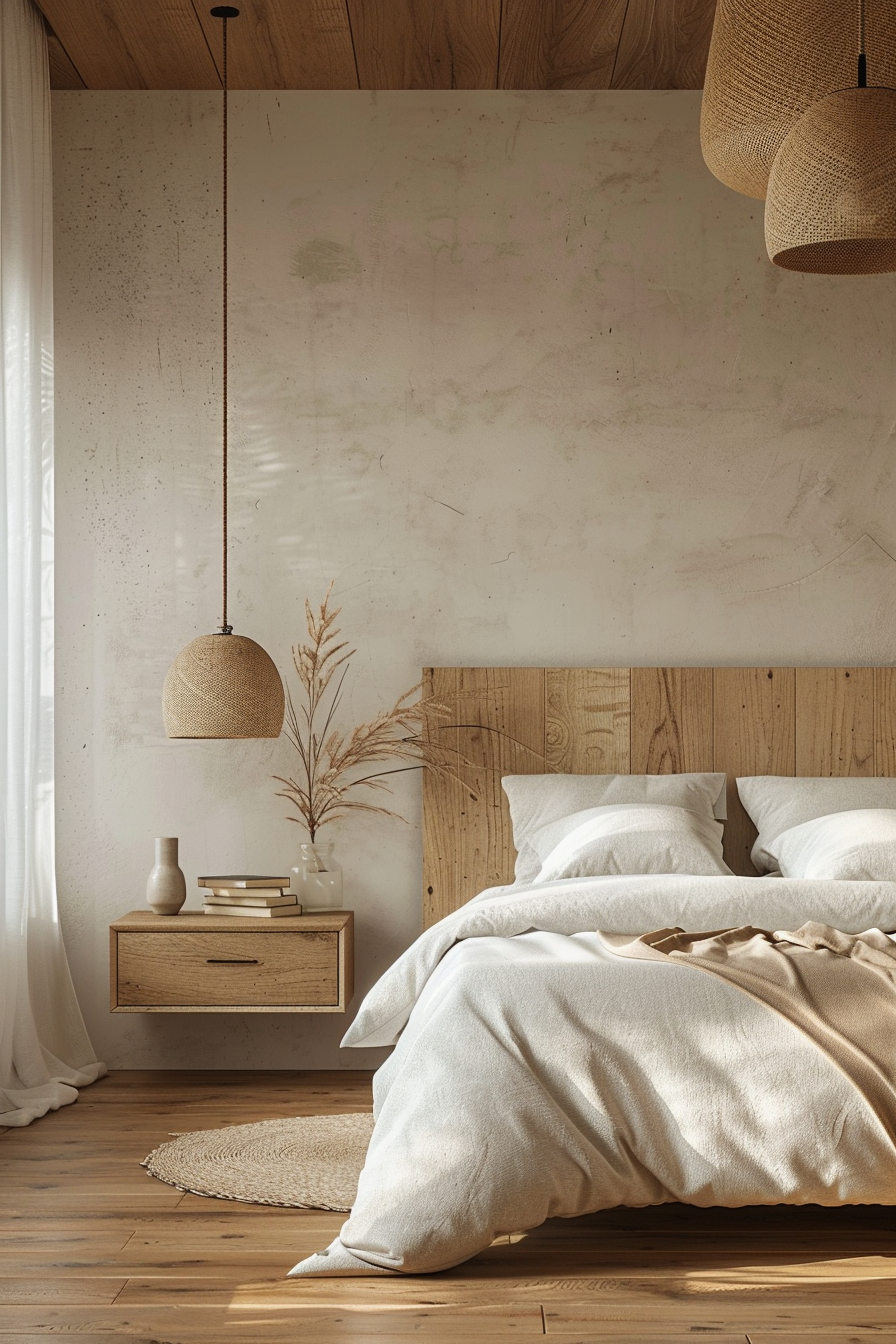
ICONBIM LLC Partners with Under Armour to Revolutionize Footwear Design and Manufacturing with Cutting-Edge BIM Technology
Federal Way, WA – October 26, 2023 – ICONBIM LLC, a leading provider of Building Information Modeling (BIM) solutions, today announced a strategic partnership with Under Armour to integrate its advanced BIM technology into the design and manufacturing process of Under Armour Men’s Boots. This collaboration promises to significantly improve efficiency, reduce waste, and enhance the overall quality of Under Armour’s renowned footwear line. For those unfamiliar, ICONBIM LLC, based in Federal Way, Washington (33301 1ST WAY S STE 200, 98003-6258, USA – reachable at 415-989-3963), isn’t your typical construction-focused BIM firm. We specialize in adapting BIM—originally used for buildings—to all sorts of product design and manufacturing. Think of it as creating a super-detailed, digital blueprint of anything before it’s even made. This lets companies like Under Armour spot problems early, tweak designs easily, and make sure everything fits together perfectly. “We’re really excited about teaming up with Under Armour,” says a spokesperson for ICONBIM. “They’re known for pushing boundaries in athletic apparel, and we believe our BIM tech can help them take their boot designs to the next level.” What does this mean for Under Armour Men's Boots? Traditionally, designing a boot like those from Under Armour involves a lot of back-and-forth. Designers create sketches, physical prototypes are made, tested, then tweaked. It's a time-consuming and expensive process. With ICONBIM's technology, things change. Imagine a completely digital boot. Every stitch, every sole component, every bit of material is modeled in 3D within the BIM environment. This "digital twin" allows Under Armour’s design and engineering teams to: Visualize everything upfront: See exactly how the boot will look and function before any physical prototype is created. No more surprises! Simulate Performance: Run virtual tests on the digital boot to see how it will hold up under different conditions—hiking, running, working on a construction site. This helps optimize the design for maximum durability and comfort. Identify Conflicts Early: Find potential issues—like parts that don't fit together properly or materials that clash—before they become expensive problems down the line. Streamline Manufacturing: The detailed BIM model provides precise instructions for manufacturing, reducing errors and waste. Accelerate Time-to-Market: By reducing the need for physical prototypes and streamlining the design process, Under Armour can bring new boot designs to market faster. Diving into the Details: How BIM Works for Footwear So, what does this BIM model actually look like for an Under Armour Men’s Boot? It’s way more than just a 3D rendering. It’s a data-rich environment. Each component of the boot—the upper, the midsole, the outsole, the laces, even the stitching—is modeled as a separate “object” within the BIM software. Each of these objects contains critical information: Material Properties: What is it made of? Leather, synthetic materials, rubber? The model specifies the exact type and properties of each material. Dimensions & Geometry: Precise measurements and shape of each component. Manufacturing Data: How is this component made? What machines are used? What are the tolerances? Cost Data: The cost of materials and manufacturing for each component. This data isn’t just for show. It’s used throughout the entire lifecycle of the boot—from design to manufacturing to quality control. Specific Benefits for Under Armour's Product Line Let’s look at some concrete examples of how ICONBIM’s technology is impacting Under Armour Men’s Boots: Enhanced Durability: By simulating stress and strain on the digital boot, Under Armour engineers can identify weak points and reinforce them with stronger materials or improved construction techniques. This means boots that last longer, even under tough conditions. Improved Comfort: The BIM model allows for detailed analysis of the boot’s fit and feel. Under Armour can optimize the shape of the footbed, the cushioning in the midsole, and the flexibility of the upper to create a more comfortable and supportive boot. Reduced Material Waste: By precisely calculating the amount of material needed for each component, the BIM model helps minimize waste during the manufacturing process. This is good for the environment and saves Under Armour money. Faster Prototyping: While physical prototypes are still needed for testing, the BIM model drastically reduces the number of iterations required. Designers can quickly test different concepts and make changes virtually, saving time and money. Better Collaboration: The BIM model serves as a central source of truth for all stakeholders—designers, engineers, manufacturers, and quality control personnel. This ensures that everyone is on the same page and reduces the risk of errors. The Future of Footwear Design & Manufacturing ICONBIM’s partnership with Under Armour is a sign of things to come. BIM technology is rapidly transforming the way products are designed and manufactured across a wide range of industries. “We see a future where all products—from boots to cars to airplanes—are designed and manufactured using BIM,” says the ICONBIM spokesperson. “It’s a more efficient, sustainable, and innovative approach.” Under Armour is clearly embracing this future, and its customers are sure to benefit from the improved quality, durability, and performance of its Men’s Boots, thanks to the power of BIM technology. Keep an eye out for the next generation of Under Armour footwear – it’s being built with the future in mind.